Oczekiwania stawiane producentom wielowarstwowych pokryć podłogowych z drewna, są coraz wyższe.Kupujący stają się coraz bardziej wymagający pod względem estetycznym, a wiele firm decyduje się na stosowanie różnych gatunków drewna, w tym drewna egzotycznego, co stwarza wiele wyzwań dla procesów produkcji.
Drewno egzotyczne wyzwaniem dla procesu klejenia
Drewno egzotyczne jest trudniejsze w obróbce i bardzo wymagające pod względem doboru kleju. Jego anatomiczna budowa i obecność różnych substancji może skutkować zmniejszoną przyczepnością, co znacznie utrudnia proces wiązania. Innym problemem jest zwiększenie wytrzymałości i trwałości posadzki wielowarstwowej ze względu na jej zastosowanie w różnych typach pomieszczeń oraz wpływ ogrzewania podłogowego. Innymi ważnymi czynnikami są umiejscowienie podłogi (czy będzie miała kontakt z wodą, czy będzie wystawiona na działanie promieni słonecznych?) oraz warunki, takie jak wilgotność i cykliczne (dzienne lub miesięczne) zmiany. Narażenie na działanie promieni słonecznych powoduje nagrzewanie się powierzchni, szczególnie w przypadku ciemnych desek podłogowych. Podczas produkcji podłóg wielowarstwowych ważne jest, aby wybrać odpowiedni klej. Dzieje się tak dlatego, że obecnym trendem są duże okna tarasowe i balkonowe, które narażają podłogi na duże nasłonecznienie, a po zachodzie słońca drastyczny i gwałtowny spadek temperatury. Stwarza to duże naprężenie termiczne, które klej wytrzymuje. W takich przypadkach wymagane są kleje zgodne z WATT ’91 (DIN EN 14257).
Sklejanie warstw i rdzeni
Ważnym aspektem jest użycie różnych rdzeni w celu zwiększenia wytrzymałości.Mogą być wykonane z litego drewna (zwykle niższej jakości), sklejki i HDF, który jest coraz powszechniejszy.Jako warstwę środkową stosuje się zwykle drewno sosnowe, świerkowe lub drewno z odpadów poprodukcyjnych warstwy wierzchniej.W przypadku sosny częstym problemem jest obecność dużej ilości żywicy lub innych wad drewna (np. sęków).Może to osłabić przyczepność i utrudnić wnikanie kleju w głąb materiału, co może spowodować osłabienie wiązania.Najczęściej uwidacznia się to dopiero podczas użytkowania podłogi.
Stosowanie rdzeni ze sklejki i HDF stwarza wiele problemów dla producentów, od procesu obróbki skrawaniem po klejenie. Stosowanie rdzeni drewnopochodnych w podłogach bardzo często prowadzi do odkształceń, takich jak zwijanie się i wypaczanie, co oznacza, że nie można używać gotowego produktu. Takie materiały wymagają od producentów stosowania klejów, które zapewniają mocne wiązanie klejowe i zapobiegają odkształceniom. Powierzchnia rdzenia HDF może stanowić kolejny problem, a mianowicie zmniejsza zdolność kleju do wiązania się z nim. Prostym rozwiązaniem byłoby zastosowanie klejów o szerokim spektrum właściwości wiążących, które bardzo dobrze przylegają do wielu trudnych materiałów (w tym do rdzeni HDF). Dla producentów podłóg wielowarstwowych korzystne byłoby, gdyby dokładnie wiedzieli, w jaki sposób ich produkty będą używane i gdzie będą się znajdować. Zwykle jednak producentom brakuje takich informacji, więc muszą uwzględnić wszystkie rodzaje możliwych zastosowań i scenariuszy, które czasami mogą być dalekie od pierwotnego przeznaczenia ich produktów. Stąd konieczność stosowania najlepszych technologii wykańczania powierzchni, obróbki i klejenia.
Znaczenie klejenia podczas procesu produkcji
Proces klejenia znacząco wpływa na jakość gotowego produktu, mimo że stanowi niewielką część kosztu produktu.Dlatego tak ważne jest, aby do łączenia materiałów używać najwyższej jakości i odpowiednio dobranych klejów. Kiilto oferuje szeroką gamę niezwykle wszechstronnych klejów do produkcji wielowarstwowych materiałów podłogowych.Stosowanie tych klejów gwarantuje uzyskanie połączenia najwyższej jakości.Coraz ważniejszym aspektem jest również bezpieczeństwo produkcji i użytkowania.Dlatego wiele klejów Kiilto posiada certyfikat M1, który gwarantuje, że emisje wszystkich lotnych związków organicznych (LZO) są na bardzo niskim poziomie, nie przekraczającym 0,2 mg / m2h.Kleje z certyfikatem M1 sprawiają, że gotowa wielowarstwowa podłoga jest bezpieczna w użyciu.
Zwiększ efetywność produkcji dzięki klejom D3 PVAc firmy Kiilto
Kiilto proponuje producentom podłóg drewnianych klej Kestokol D 320 HF, w którym zawartość formaldehydu spada poniżej 20 ppm, zgodnie z normą ISO 15373. Klej ten to alternatywa dla zawsze popularnych produktów mocznikowo-formaldehydowych bez uszczerbku dla wydajności wiązania ijakości.Jest to doskonały klej do produkcji podłóg na liniach pras na gorąco i coraz częściej używanych prasach wysokiej częstotliwości (HF).Zapewnia bardzo wysoki poziom produktywności z czasem prasowania do 40 sekund i wydłużonym czasem otwartym, co pozwala na ciągłą produkcję, która jest zawsze „online”.Ten produkt charakteryzuje się wysoką odpornością termiczną WATT ’91.
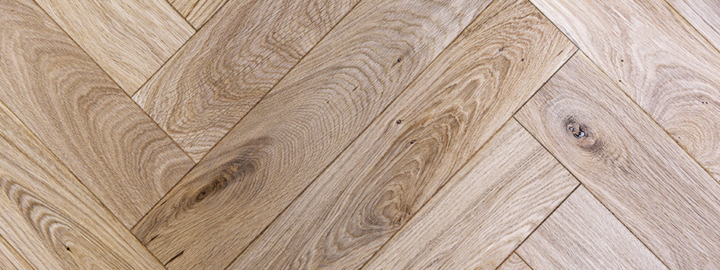